Does Misalignment Cause Vibration
The correlation between misalignment and vibration in machinery is a topic of considerable interest to engineers and maintenance professionals. Misalignment, the improper positioning of machine elements, can result in uneven forces and increased friction, leading to discernible vibrations. These vibrations not only signify the existence of misalignment, but also contribute to accelerated wear and tear, increased energy consumption, and heightened maintenance costs. However, is it accurate to infer that misalignment is always the primary cause of such vibrations? Let’s explore this further, and examine the intricate dynamics involved.
Understanding Machine Misalignment
Machine misalignment, a common challenge in industrial operations, is an intricate issue that warrants thorough understanding. It refers to the inaccurate positioning of machine components relative to one another, leading to suboptimal performance, increased energy consumption, and premature equipment failure. The complexity of the issue is underscored by the variety of factors that can cause misalignment, including incorrect installation, operational forces, and natural wear and tear.
Alignment techniques come into play to rectify misalignment, employing precision measurement tools to guarantee machines are correctly aligned within specified tolerance ranges. These techniques vary, depending on the machine type and configuration. For instance, shaft alignment techniques are commonly used for rotating machinery, such as pumps and motors, while geometric alignment is suitable for stationary equipment.
Laser alignment, an advanced alignment technique, uses laser beams and detectors for precision measurement. It offers a high degree of accuracy, making it ideal for complex and large-scale industrial applications. However, it requires skilled personnel for operation and interpretation of results.
Understanding machine misalignment entails a thorough grasp of the equipment, alignment techniques, and precision measurement methodologies. This knowledge forms the basis for effective alignment procedures, contributing to enhanced operational efficiency and equipment longevity.
Common Signs of Misalignment
Recognizing the signs of misalignment is a fundamental aspect of maintaining operational efficiency and preventing premature equipment failure. Misalignment detection can be a complex process, requiring an extensive understanding of the machine operation and specific alignment tools.
Common signs of misalignment include abnormal noise, excessive heat, and increased energy consumption. Noise is often the first noticeable indicator. It can manifest as a high-pitched squeal or a low hum, indicating potential misalignment between components. Excessive heat, on the other hand, results from increased friction caused by misalignment. Heat can degrade equipment materials, leading to further complications if not addressed promptly.
Increased energy consumption is a less obvious but equally significant sign. Misalignment forces equipment to work harder to achieve the same output, leading to higher energy usage. Monitoring energy consumption can aid in early misalignment detection, preventing costly repairs and downtime.
Vibration: A Symptom or Cause?
As we turn our attention to the issue of vibration, it is essential to discern whether it is a symptom or cause within the context of misalignment. The origin of vibration, its relationship with misalignment, and the strategies to address related issues will be critically evaluated. This analysis allows us to comprehend the intricate dynamics between misalignment and vibration, providing insights for effective diagnostic and rectification procedures.
Understanding Vibration Origins
In the domain of industrial mechanics, understanding the origins of vibration, and distinguishing whether it acts as a symptom or a cause, is of utmost importance. Vibration sources are numerous and can be broadly classified into two categories: internal and external. Internal sources are inherent to the machinery, such as imbalances in rotating parts, gear misalignment, or bearing defects. External sources, on the other hand, involve factors like environmental disturbances or improper installation processes.
Alignment techniques play a crucial role in mitigating internal vibrations. Proper alignment guarantees uniform distribution of forces across all machine components, thereby reducing the chances of excessive vibration. However, even with perfect alignment, it is impossible to eliminate vibration completely due to the dynamic nature of mechanical operations and the presence of external vibration sources.
Misalignment as Vibration Source
Misalignment, as a significant internal vibration source, merits a concentrated examination. The vibrational energy created due to misalignment in machinery components can lead to detrimental effects on the machine’s operational efficiency and longevity. Misalignment, irrespective of its form, whether angular or parallel, triggers a series of vibrations that can be detected through vibration analysis.
Understanding the role of misalignment as a vibration source demands an exploration of specific areas:
- Misalignment Types: Both angular and parallel misalignment can produce vibration, albeit with different characteristics.
- Vibration Patterns: Misalignment triggers specific patterns of vibration, which can be identified through vibration analysis.
- Equipment Impact: The induced vibrations from misalignment can lead to increased equipment wear, energy consumption, and potential premature failure.
- Alignment Techniques: Proper alignment techniques can correct misalignment and thereby reduce vibrations.
- Vibration Analysis: This is a vital tool in diagnosing misalignment, by interpreting the specific vibration patterns caused by various types of misalignment.
Thus, misalignment is not just a potential source of vibration, but a vital factor that warrants a meticulous analysis to maintain machinery efficiency.
Addressing Vibration Issues
Addressing vibration issues effectively requires us to explore deeper into the nature of vibration itself. Vibration, often perceived as a symptom, can indeed be a root cause, complicating the detection and resolution of underlying issues. Vibration analysis, a systematic method to understand and break down the complex variables of vibration, becomes indispensable in this situation.
This analytical approach entails the recording, examination, and interpretation of vibrational patterns. Such patterns may signify deviations from the norm, indicating misalignment or other mechanical problems. The data acquired from vibration analysis is meticulous and valuable, enabling an accurate diagnosis of the source of vibration, be it misalignment or otherwise.
Once we identify the source, addressing the issue becomes more feasible. This is where alignment techniques come into play. These methods guarantee a proper arrangement of the interconnected machine components, reducing the potential for misalignment-induced vibrations. By using precision tools and procedures, alignment techniques can rectify misalignment, thereby mitigating the associated vibration issues.
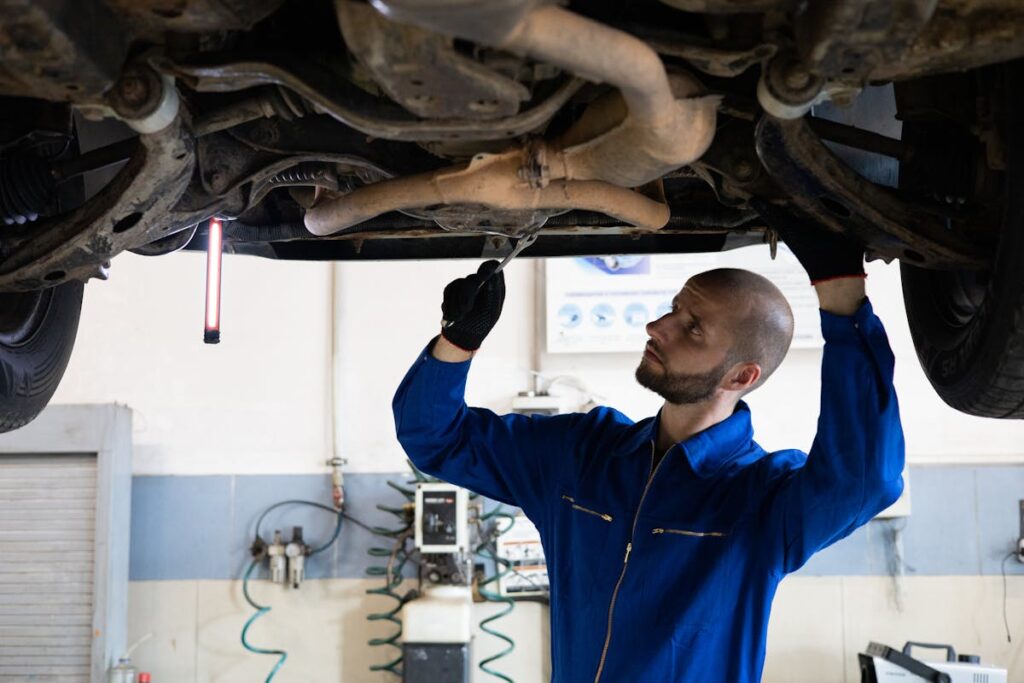
Correlation Between Misalignment and Vibration
A significant correlation exists between misalignment and vibration in mechanical systems. Misalignment consequences can be severe, leading to increased vibration levels, which often cause damage and inefficiencies in the operation of machinery. Consequently, vibration analysis becomes a critical tool in detecting and correcting issues arising from misalignment.
From an analytical perspective, the correlation can be detailed as follows:
- Misalignment leads to an uneven distribution of load across the machine components. This uneven load distribution can cause oscillatory motion – or vibration – in the system.
- The magnitude of vibration typically increases with the degree of misalignment. This can be detected and quantified through vibration analysis.
- Misalignment can cause an increase in temperature due to friction, leading to thermal expansion and added vibration.
- Vibration due to misalignment can lead to premature wear and tear of components, including bearings and seals, leading to frequent breakdowns and increased maintenance costs.
- Ultimately, vibration due to misalignment can lead to noise pollution, affecting the working environment and potentially violating noise regulations.
Case Studies: Misalignment Leading to Vibration
To further elucidate the relationship between misalignment and vibration, we now turn our focus to several case studies that clearly illustrate the consequences of such mechanical issues. These real-life incidents provide tangible evidence of the damage misalignment can inflict through induced vibration. Finally, we will examine the strategies employed to mitigate these vibrations by implementing precise alignment techniques.
Understanding Misalignment and Vibration
Delving into the domain of misalignment and vibration, we find a complex interplay of mechanical and physical phenomena at work. Misalignment effects, although seemingly minor, can greatly influence machines’ operating efficiency, causing vibrations that can lead to failure in extreme cases.
The misalignment-vibration relationship can be better understood through the following points:
- Misalignment causes uneven distribution of forces across machine components, leading to vibration.
- These vibrations, if left unchecked, can result in wear and tear of components, reducing the machinery’s lifespan.
- Vibration analysis can provide insights into the degree of misalignment, helping in timely identification and correction.
- Misalignment effects are not only limited to vibrations. They also lead to energy loss, increased noise, and excessive heat generation.
- Vibration reduction is a direct consequence of proper alignment and balances in machinery, leading to improved efficiency and longevity.
Understanding the intricate relationship between misalignment and vibration is essential for maintaining machinery’s best functioning. It is a step towards proactive maintenance, reducing unexpected downtime and ensuing costs. This comprehension is also a key to designing better, more robust machinery in the future.
Real-life Misalignment Incidents
While it is beneficial to understand the theoretical aspects of misalignment and vibration, examining real-world incidents can provide a deeper comprehension of these phenomena.
In the industrial sector, one compelling instance of misalignment leading to vibration occurred in a pulp and paper mill. The facility, which relied heavily on a series of rotating equipment, experienced severe vibrations in their machinery. Detailed analysis and diagnostics revealed that the root cause was misalignment, specifically in the high-speed coupling of a critical pump.
The misalignment caused erratic rotational movement, leading to erratic vibrations that greatly disrupted operations. The industry impacts were palpable. The vibrations resulted in frequent machinery shutdowns, negatively impacting production schedules and causing substantial economic losses.
Similarly, in the energy sector, a notable case involved a gas turbine generator. The generator experienced excessive vibration levels during operation. Investigations pinpointed the cause to a misalignment issue between the generator and the turbine. Like the previous real world example, this misalignment-induced vibration led to operational inefficiencies, unscheduled downtime, and considerable financial implications.
These incidents underscore the critical need for proper alignment in mechanical systems to prevent adverse vibrational effects and guarantee peak performance.
Mitigating Vibration Through Alignment
Drawing on the insights gained from the aforementioned real-world incidents, it is clear that mitigating vibration in mechanical systems hinges greatly on achieving precise alignment. Indeed, the implementation of precision alignment techniques can greatly contribute to vibration reduction, improving the overall efficiency and lifespan of the system.
A series of measures can be undertaken to combat misalignment and its associated vibrations, including:
- Utilizing advanced alignment tools that can facilitate accurate measurements and adjustments.
- Conducting regular vibration analysis to detect early signs of misalignment and prevent further damage.
- Implementing precision alignment protocols during the installation and maintenance of machinery.
- Investing in vibration monitoring systems to continuously track the health of the machine.
- Providing alignment training for operators and maintenance personnel to enable swift vibration troubleshooting.
These strategies not only reduce the risk of misalignment-induced vibration but also minimize downtime, increase operational efficiency, and promote a safer work environment. Ultimately, the role of alignment in mitigating vibration cannot be overstated; it is a critical aspect of machinery maintenance and operation that demands a meticulous and proactive approach.
Mitigating Vibrations Through Proper Alignment
One often overlooked aspect in machinery operations is the role of proper alignment in mitigating vibrations. Proper alignment techniques are indispensable for vibration control, as vibrations can lead to numerous negative outcomes including increased wear and tear, reduced operational efficiency, and even catastrophic machine failure.
It is important to understand that alignment is not a one-size-fits-all task. The alignment techniques used must be tailored to the machinery in use, taking into account factors like the machine’s design, operational conditions, and load requirements. For instance, the alignment for a high-speed turbine will differ from that of a low-speed pump.
When alignment is performed adequately, it minimizes the vibration levels produced during operation, which in turn reduces the risk of damage to other parts of the machine. This can greatly improve the machine’s lifespan and operational efficiency.
Maintenance Practices for Alignment
Implementing robust maintenance practices for alignment plays a vital role in guaranteeing the smooth operation of machinery. Proper alignment practices can markedly reduce the risk of equipment failure, decrease energy consumption, and improve overall operational efficiency. In order to achieve this, a combination of alignment tools, techniques, and best practices should be employed.
- Utilizing advanced alignment tools such as laser alignment devices and alignment software can provide high levels of accuracy and ease of use.
- Regular alignment audits are essential to verify alignment standards are maintained and identify any potential issues early.
- Alignment training should be provided to make sure that staff are knowledgeable and skilled in alignment procedures.
- Implementing a schedule based on alignment frequency is essential. This guarantees that alignment checks and adjustments are made at appropriate intervals.
- The use of precise alignment measurement techniques is paramount in guaranteeing the correct alignment of machinery components.
These maintenance practices, when implemented and adhered to, not only enhance equipment longevity but also contribute to the reduction of unwanted vibrations. Proper alignment can indeed prove to be a potent tool in vibration mitigation.
Impacts of Ignoring Misalignment
Neglecting the issue of misalignment can have severe repercussions on machinery performance and longevity. The operational efficiency of the equipment can drastically reduce, leading to productivity loss. Misalignment can cause excessive vibration, leading to wear and tear, eventually shortening the equipment lifespan.
Ignoring misalignment also poses significant safety concerns. The increased vibration can cause components to loosen or break, potentially leading to catastrophic failures and posing a risk to personnel.
The cost implications of ignoring misalignment are substantial. The long term damage caused by misalignment often necessitates expensive repairs and can lead to an increase in unplanned downtime. The repair expenses can be considerable, especially if key components or the entire machine need replacement.
Moreover, misalignment results in maintenance challenges. It complicates troubleshooting efforts, as the symptoms of misalignment can often mimic other issues. Consequently, maintenance teams may spend unnecessary time and resources attempting to resolve the wrong problem.
Frequently Asked Questions
What Are the Costs Associated With Fixing Machine Misalignment?
The costs associated with fixing machine misalignment include direct repair expenses and indirect costs from downtime. Optimized maintenance strategies can help mitigate these costs by reducing the frequency and impact of misalignment incidents.
Could Machine Misalignment Be a Safety Hazard for Operators?
Yes, machine misalignment can indeed pose a safety hazard for operators. This is mainly due to the vibration hazards it can create, which may result in equipment instability, affecting operator safety and overall productivity.
Does Misalignment Affect Machine Efficiency and Output Quality?
Yes, misalignment can greatly impact machine efficiency and output quality. It can lead to increased power consumption, accelerated wear, and diminished product quality, necessitating periodic vibration analysis and precise alignment techniques to guarantee peak performance.
Are There Specific Industries That Face More Problems Due to Misalignment?
Yes, specific industrial sectors such as manufacturing, energy, and maritime industries often face more problems due to misalignment. Regular alignment monitoring is vital in these sectors to guarantee peak machine performance and minimize operational disruptions.
How Often Should Routine Checks for Misalignment Be Performed?
The frequency of routine checks for misalignment largely depends on the equipment usage. Regular alignment methods and vibration analysis should be performed at least bi-annually for peak machinery performance and longevity.